Software Integration
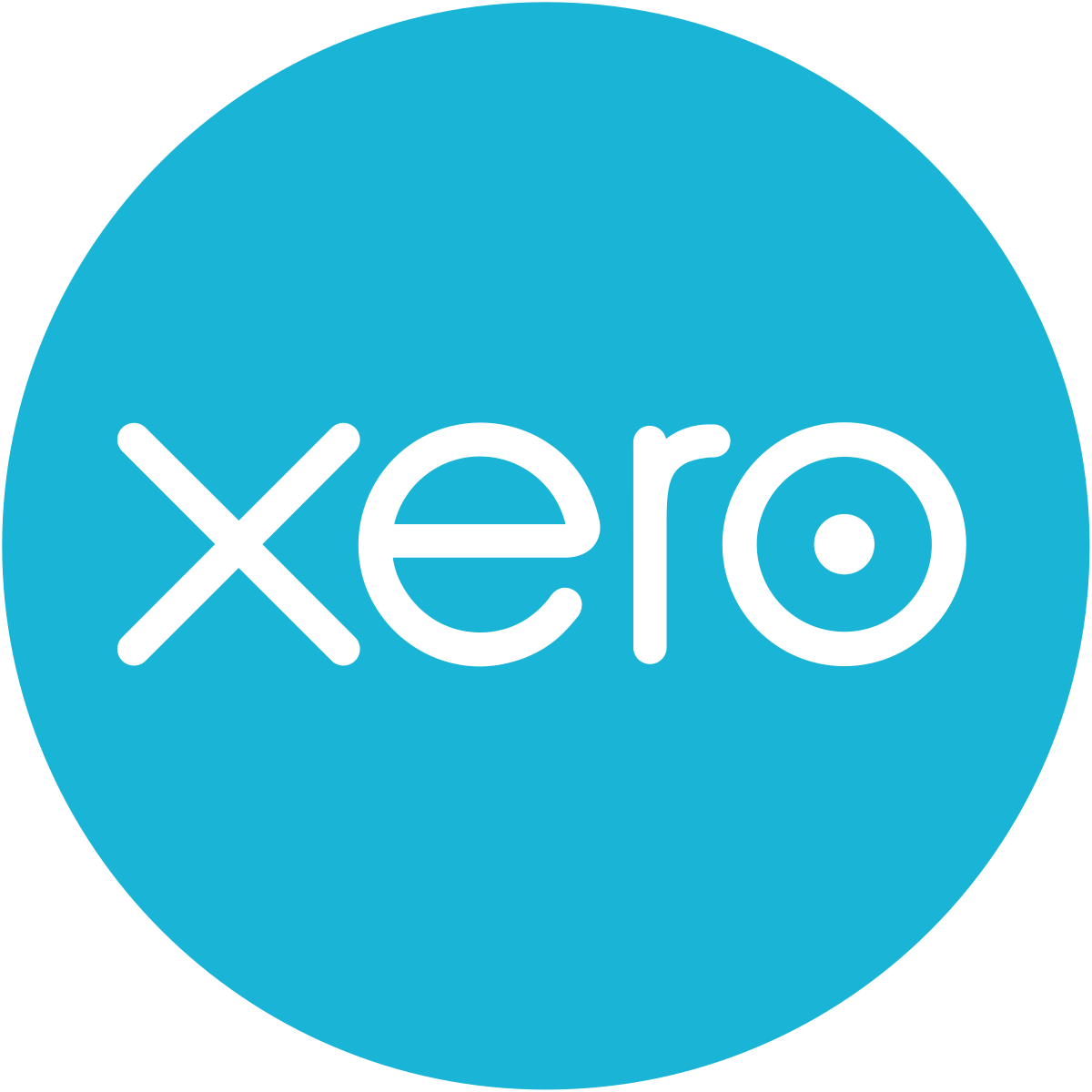
What can Cabinetry.Online’s Xero Integration do?
In a nutshell, the main thing this integration will do is save you time. It does this by simplifying your invoicing process.
Syncing your customers
Link Existing Customers: Matches Cabinetry.Online customers to Xero contacts using email addresses.
Export Client List: Export your full client list from Cabinetry.Online in a format compatible with Xero.
Customising your invoices
Set Default Account Code: Assign default chart of accounts code for sales.
Set Invoice Prefix: Customise invoice prefixes (e.g., ABC- instead of INV-).
Use Job Numbers as Invoice Numbers: Maintain consistency by using Cabinetry.Online job numbers as Xero invoice numbers.
Default Branding: Choose default branding for invoices if multiple options are set up in Xero.
Default Days Due: Set default payment terms for invoices, or bring Xero’s invoice terms to Cabinetry.Online.
Other automated actions
Check for Existing Contacts: Automatically checks for existing contacts in Xero when accepting a job.
Create New Customer Contacts: Prompts Xero to create a new contact if one doesn’t exist.
Auto-Populate Invoices: Invoices are automatically filled with key information like job number and description.
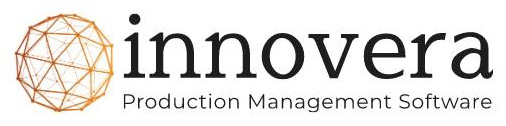
What can Cabinetry.Online’s Innovera Integration do?
Our integration with Innovera’s Production Assistant enhances your operational efficiency by streamlining how you handle parts and hardware reports generated from Cabinetry.Online’s production software.
Integration Details
CSV Report Creation: Cabinetry.Online jobs are downloaded and processed through our production software, which then generates a CSV report containing parts and hardware data.
Production Assistant Ingestion: This CSV report can be directly ingested into Innovera’s Production Assistant, a robust part tracking program.
Workflow
Job Download: Cabinetry.Online job gets downloaded and processed through our production software.
File Creation: Our production software creates a file for nesting the job and also generates a part report for Production Assistant.
G-code and Labeling: The software produces the G-code to nest all parts and labels them with individual barcodes.
Barcode Scanning: Scanning the barcode allows Production Assistant to identify the part and indicate its correct location.
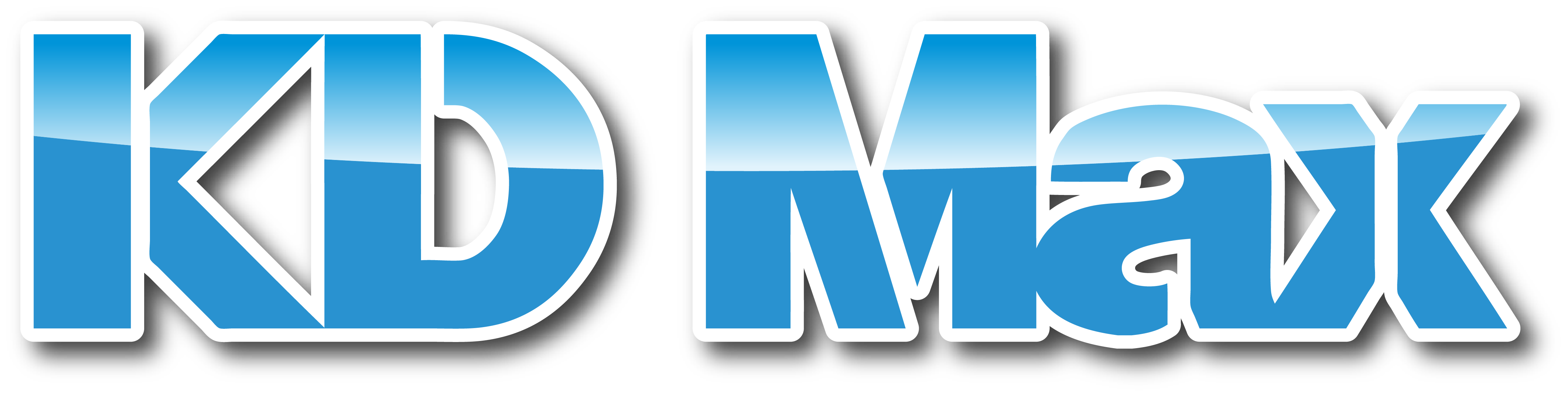
What can Cabinetry.Online’s KD Max Integration do?
Your clients will be able to import the cabinetry information from their KD Max designs directly into their online orders with the click of a button, saving them time from having to reinput all the cabinetry and dimensions from their jobs.
Workflow
Design: A client creates a design using KD Max Design Software.
Specification Setup: The client sets up their default specifications (Materials, Hardware, Margins etc.) for a project in your online portal.
Import: In KD Max, clients output an XML file for their design, and then upload it into the online ordering platform.
Merging: The product types, and dimensions from KD Max are merged with the default specifications from the client’s project.
Confirm and Quote: A list of products is generated in the online project for client approval. Products are confirmed and a quote is generated instantly.